Why does the bioreactor need an impeller?
The primary function of the impeller is to continuously stir the contents of the vessel, ensuring homogenous mixing and therefore providing the cells with consistent access to the nutrients within. Certain impellers function by maximizing energy transfer whilst balancing the shear forces within the bioreactor (Wong & Zhong, 2007). The position and size of the impeller depends upon the size of the bioreactor. In general, bioreactors with a large height to diameter ratio will use more than one impeller to guarantee sufficient aeration and agitation for the cells/microorganisms inside the vessel.
What types of impellers are used for bioreactors?
Impellers can be categorized by the flow direction in which the fluid is mixed. Four classifications exist that allow up or down regulated flow direction: axial flow, radial flow, mixed flow, and distributed flow.
- Pitch-blade or marine impellers are commonly used for cell culture processes and generate an axial flow. This occurs when the cell suspension is pumped in one direction and sucked from the opposite side parallel to the axis shaft. Marine impellers are known for their shear sensitivity and efficient mixing at low impeller tip speeds.
- Radial flow creators, such as Rushton impellers, pump the fluid radially outwards and suck it in from both sides of the impeller in an axial flow direction. This type of impeller is commonly applied for microbial fermentation processes.
- Angled pitch-blade impellers result in a mixed flow, where the vertically angled blades move the liquid in axial as well as radial directions.
- Distributed flow is produced by using helical type impellers, which provide equally distributed shear plane as well as gradients in all directions. Such impellers are frequently used for solid substrate or high viscosity fermentations (Peker et al., 2008)
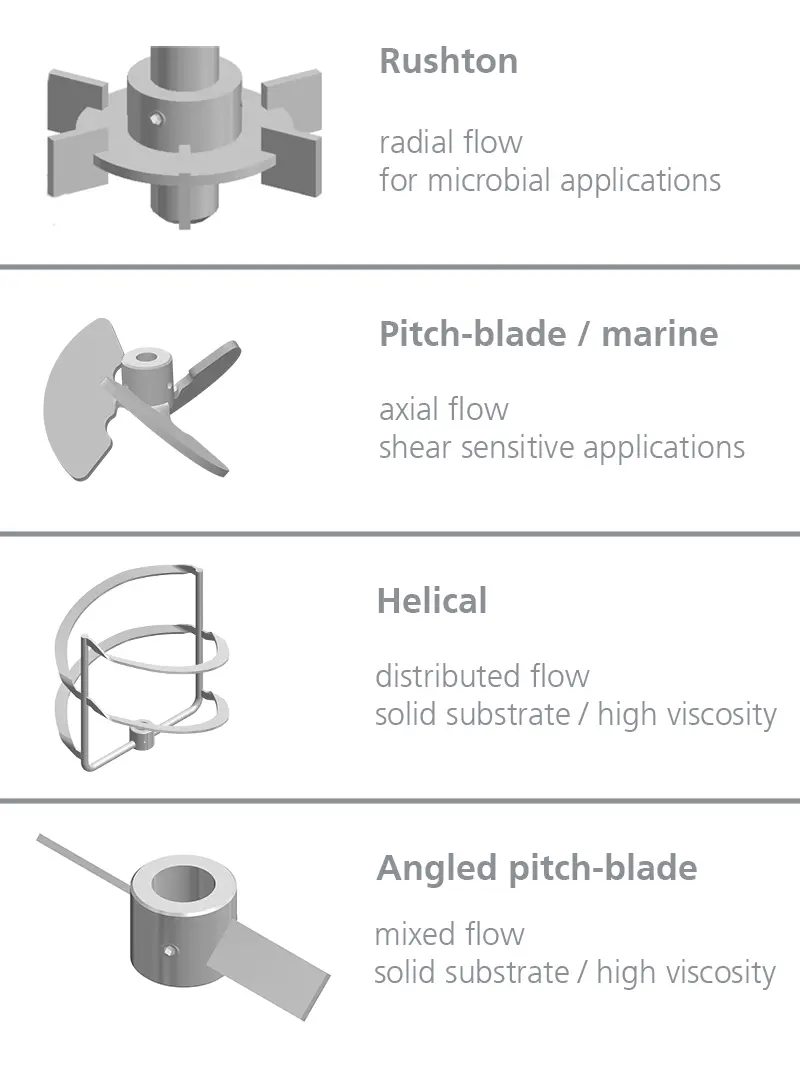
Depending upon the application, a combination of impeller types is also possible to increase mixing characteristics and reduce shear force.
How to choose the right impeller for your bioprocess
To ensure healthy growth of cells, the impeller needs to stir the mixture of substrate, cells, and oxygen homogenously. Furthermore, it is important to choose the right impeller type to provide a high yield and good quality of your product. This is not always a straightforward decision to make. Below, we have outlined the major parameters to consider.
Mixing time
The mixing time of a bioreactor is a key factor for consideration. It describes how long a liquid needs to be stirred as well at which speed to obtain an optimal state of homogeneity. The duration is often determined using a coloring method: A starch solution is mixed with an iodine-potassium-iodine solution tempered at 25 °C. To this solution-mixture, sodium thiosulfate is then added, and the reaction time is recorded until the solution becomes clear. This determines the time it takes to achieve a homogenous solution. The shorter the time, the better the mixing properties of the impeller and the balance of shear force within the bioreactor. Cell culture processes typically show longer mixing times compared to microbial fermentations. This is due to the slower speeds and the application of different impeller types, which cause less turbulence.
Power input
Power input can be determined through the torque that acts on the impeller shaft while it is rotating. The power input is an important factor due to its association with shear forces, and is also a key parameter during scale-up processes. Since the impeller can also affect the quality of the product and cell growth, it is valuable to determine the power input. Other techniques exist including electrical power draw or calorimetric methods. Listed below are the formulas and corresponding explanations of specific variables for calculating power input.
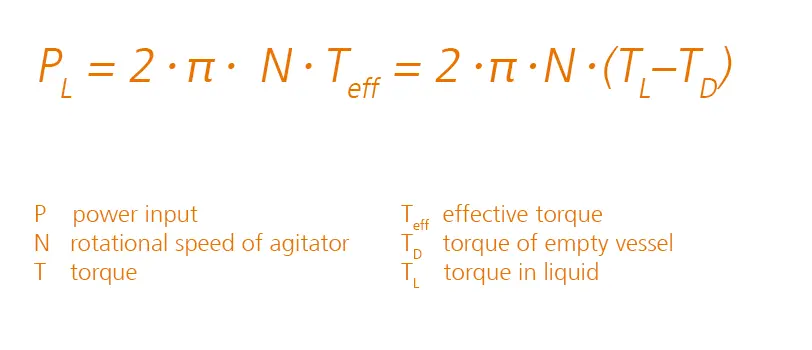
The power input can be calculated by measuring the torque, especially the effective torque which includes the losses arising during agitation (bearings, seals, and motor). The effective torque is defined as the difference between the torque measured in the empty vessel and in the liquid (Kaiser et al., 2018).
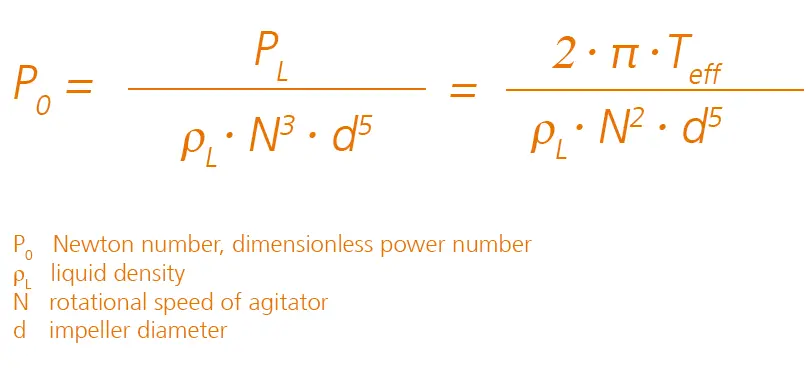
The dimensionless power number is described by the density of the liquid and the impeller diameter. It can be applied to compared different agitators (Kaiser et al., 2018).

The power number is a function of the Reynolds number, which becomes constant under fully turbulent conditions (Kaiser et al., 2018).
A high power input number results in higher energy input into the system, which results in good mixing and oxygen transfer. Therefore, a well-designed impeller is characterized by achieving similar levels of power input with slower stirring speeds. This is especially important for sensitive cells.
Dimensions
When selecting a specific impeller for your application, be aware that the impeller needs to have a specific off-bottom clearance and an appropriate impeller size in relation to the vessel size to ensure homogenous and shear sensitive mixing. In addition, the position and type of sparger play a key role in the performance of the impeller. The ratio of liquid height to vessel diameter also influences the impeller’s performance. Therefore, large bioreactors will use more than one impeller to allow homogeneous mixing and aeration within the whole bioreactor (Wang & Zhong, 2007). To find the appropriate dimensions in accordance with the vessel size, the first two parameters above can be very useful points to consider.
Eddy size
Another parameter especially useful for cell culture processes is the eddy size. During cultivation, cells are exposed to a turbulent fluid flow. If this turbulence is sufficiently strong, that flow will lead to cells being damaged or even killed by fluid-mechanical forces. Excessive agitation generates eddies of small enough size but sufficient energy to cause damage to the cells. According to Kolmogorov eddy size model, eddies that are smaller than the cell diameter are considered to damage the cells. Therefore, a recommendation is to operate the impeller in a way that the Kolmogorov scale remains greater than the cell diameter.
Maximum energy dissipation
The maximum energy dissipation alone will not necessarily give you much input but comparing it with the power input and the tip speed of the impeller it can lead to useful characterization information. If you are investigating the maximum energy dissipation in relation to the power input, an optimal impeller should achieve the same power input, but with lower stirring required, which means less energy loss. As a rule of thumb, smaller relations between the maximum and the average energy dissipation rate are beneficial.
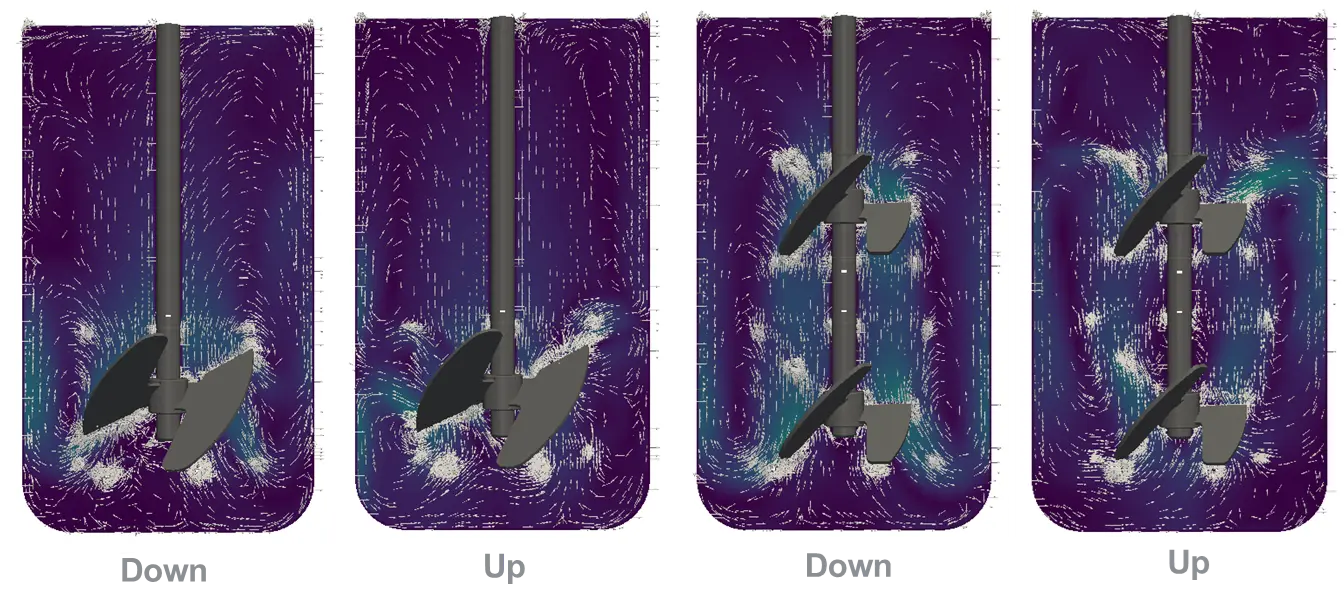
Minifors 2 Cell CFD simulation comparing one and two downwards as well upwards impellers. Results showed a lower maximum energy dissipation for one impeller, downwards. The Computational Fluid Dynamics (CFD) is a powerful engineering tool used to perform calculations, in which it is possible to simulate flow directions and power input.
Summary
It is very important to carefully decide and evaluate the impeller according to your application. It will impact the homogeneity of your suspension and therefore the heat and mass transfer within the cells, leading to a big influence on product quality and yield. The suggested impeller characterization methods should help you to get a clearer picture of your impeller design and support you in your decision. If a bioreactor s characterized by a high power input and short mixing time, then it shows that the impeller is cleverly designed providing good prerequisites for a successful cultivation.