1991: Focus on fungal and microbial applications
The Multitron development dates to the 1990’s and came from the need for maximum shake flask capacity for the minimum space in the laboratory. In previous decades, the need for high capacity and throughput was met by free-standing, large shakers housed in constant-temperature rooms. The main application for these units was often large-scale screening for antibiotics. These systems were simple, effective for their main task but extremely inflexible for accommodating several users with different needs e.g., different growth temperatures. The alternative, an incubator shaker was more flexible, but lacked capacity, both in number of flasks and their maximum size.
The first Multitron provided a “game changer” in that it made use of vertical space in the laboratory by stacking up to three incubation chambers. This provided its own design challenges to keep the top deck accessible, providing easy flask handling, prevent any spillages from moving down the stack, and allowing easy access for cleaning and servicing. This system was a genuine revolution and met the changing needs of researchers engaged in microbial work. However, applications were changing with the rise of cell culture for mammalian or insect cell lines.
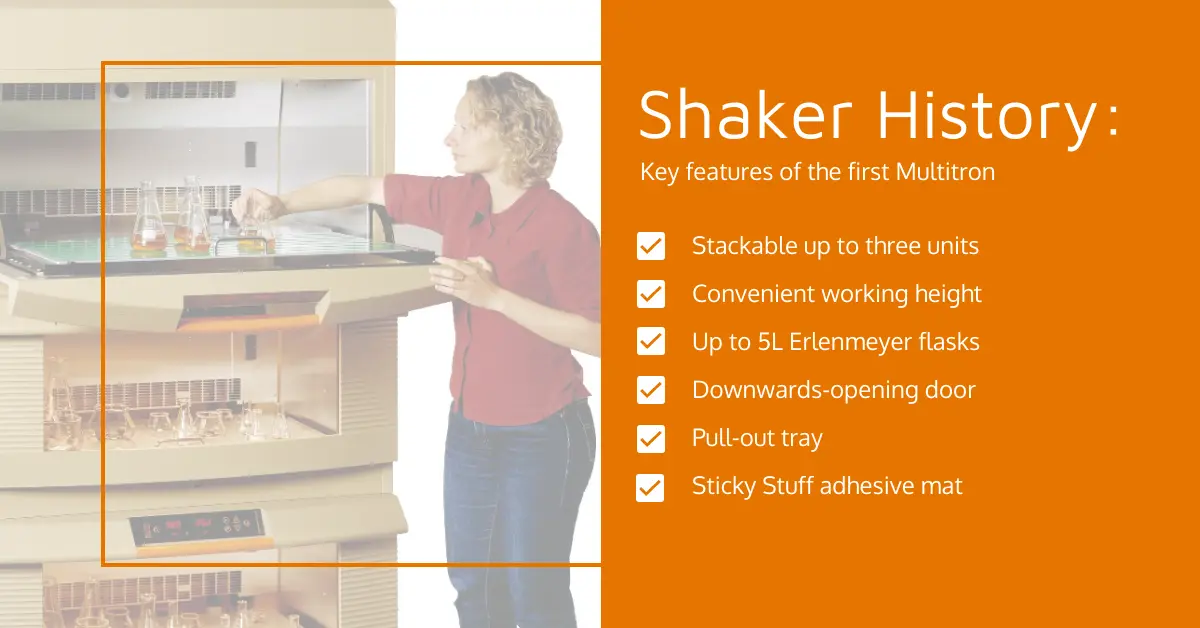
2008-2011: Cell culture applications come to the fore
By the early 2000’s, the need for growth of mammalian and insect cells in suspension culture was clear. Microbial and fungi/yeast hosts for recombinant protein production were limited in their ability to provide complete glycosylation. Also, production of viral vectors for vaccines and recombinant work using both insect and mammalian cells were common.
This led to a new generation of Multitron with a larger 50 mm shaking throw for gentle mixing plus the ability to measure and control parameters such as gassing with CO2 and percentage relative humidity. The excellent temperature distribution, a certified antimicrobial surface and options such as darkening for insect cells infected with Bacculovirus made the Mulitron the “ideal home” for these cultures.
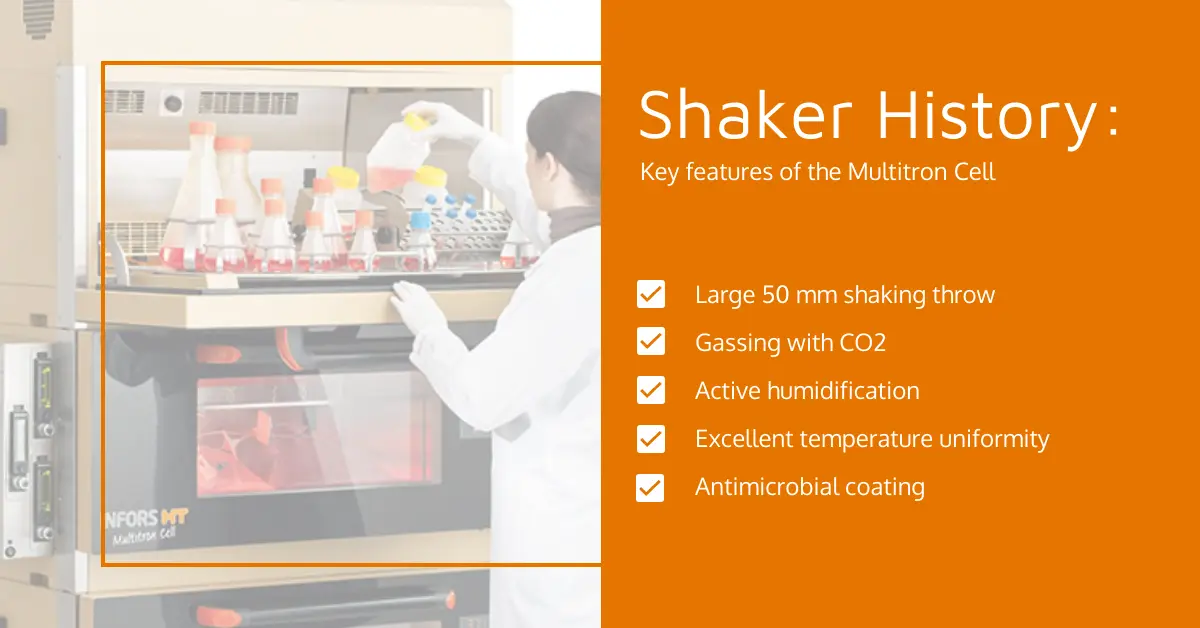
2012-2017: Multiple, parallel experiments and green applications
Then, things changed and applications such as algal biofuel and massively parallel screening in microtiter plates came to the fore. The need for thousands of screening experiments to provide rapid screening for specific biological activity drove an increased use in 96-well plates. They needed special options and adaptation to accommodate large numbers per chamber and to stop wells drying out over time. Providing adequate mixing for oxygen transfer was an issue in the smaller wells. A special high speed, short throw drive system solved this problem.
Next to the “classical” technical shaker features, influencing culture growth and productivity, usability topics have become more popular from the mid 2010’s onwards. Serial communications gave way to networked connectivity to bioprocess software for logging, analysis, and validation of shaker-based processes. An incubator shaker which could be qualified like a bioreactor for such validated process was a real revolution this time around. Suddenly, the results of screening could be taken to small scale clinical trials with the output from a single, stacked system.
When biofuel applications using photosynthetic bacteria and algae to produce fermentable sugars, the Multitron evolved to meet these requirements, yet again. LED lighting to encouraged growth of phototrophic cell lines with special spectra.